HTI, specialist in lab and manufacture automation
Opening, filling and labeling micro-screw tubes
Convey 180 uncapped tubes. Take liquid from a bottle and distribute into each tube. Pick up screw caps from a tray, seal each tube and check by sensor. Apply a label to each tube. Insert the tubes to racks, starting at position X on rack Y. HTI Automation provides solutions for such or similar lab workflows.
The company specializes in processing micro-screw tubes in machines. The X-TubeProcessor series has been designed for opening and closing tubes as standard processes. It can be modularly expanded, for example for sorting, filling, scanning or outsourcing tubes. If tubes have to be labeled after filling, the choice are label printers, print and apply systems or laser marking systems by cab, depending on the operation.
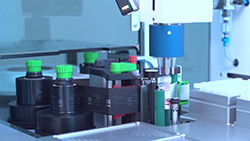
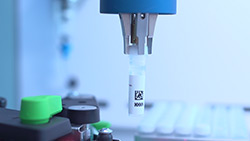
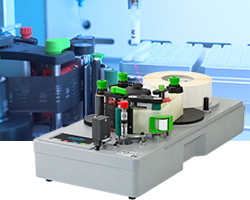
"cab", says Frank Heimberg, "has become a major partner for us in recent years." He is the Engineering Project Manager at HTI and highlights two arguments: "First, cab is a German manufacturer. Such direct contact is essential. As developers, we appreciate the wide range of cab solutions. It enables us to satisfy all customer demands."
HTI configures for pharmacists in research, food and veterinary diagnostics custom-made automats, operated stand-alone or in an automated lab system. In labs, reagents are a key for detecting elements or compounds. There may be no substitutes for samples. Values are accordingly high. Added to these are directives on pharmaceutical manufacture and data protection, such as issued by the European Commission and the Food & Drug Administration. Any machine delivered by HTI to a customer has proven full functional stability in tests exerted by technicians with a maximum of 1,000 tubes.
See and read in the following four machine samples dedicated to labeling tasks.
X-TubeProcessor Flex and HERMES Q
Dispensing liquids from containers into small vessels is a central task of automated filling. There must be no contamination. Liquids must be accurately rated and vessels be reliably labeled. Planned throughput and stable products are challenges of automated manufacture.
The X-TubeProcessor series enables fully automated tube and liquid handling with a wide range of processes in
labs and manufacture. The Flex machine type is provided in constructional widths 120 cm to 200 cm, thus particularly flexible and scalable in function and throughput. If requests are as mentioned at the beginning of this
report, cab HERMES Q systems are the choice for tube labeling. They print and automatically apply labels in one
operation. Interfaces and Industry 4.0 protocols allow for integration to a network.
- X-TubeProcessor Flex and HERMES Q: 96 tubes processed within 25 minutes
Thermal transfer printing is economical in particular with large label volumes. There is no waiting for colors to dry, as is the case with inkjet. Proper materials provided, thermal labeling remains legible on tubes during processing, inspection, picking, stock and transport. Other print methods are more sensitive. HERMES Q printers can be combined as desired with a cab standard applicator, a robot or any other module suitable for application. Filling, screwing and labeling 96 tubes with an X-TubeProcessor Flex takes about 25 minutes in serial processing. Cycles are shorter in parallel operation, depending on the modular configuration.
X-TubeProcessor Smart and AXON 1
Set up a maximum of six racks with a total of 288 tubes, start the machine, done: Using an X-TubeProcessor Smart, screwing, dispensing and labeling takes less than an hour in serial processing. Its dimensions 80 cm x 70 cm x 85 cm allow operation even on spots where space is limited.
As for tube labeling, HTI installs AXON 1. This print and apply device has been developed by cab specifically for tubes or vials with diameters seven to 26 mm (as much as 38 mm may be possible upon request) and lengths 20 mm to 130 mm. These are inserted in vertical orientation from the top. 600 dpi, high contrast and sharp-edged print images allow small batch numbers or codes be verified by eye or scanners. The labels are applied to vessels after printing. Cycles of labeling take less than two seconds.
- External cab control panel, touch function,
integrated to a X-TubeProcessor casing
- X-TubeProcessor Smart and AXON 1:
tubes with diameters seven to 26 mm
Data can be transferred via RS 232, USB, Ethernet, WLAN or Bluetooth. Flat design facilitates installation to a X-TubeProcessor. If sterility is requested in the processor, operating the printer by touchscreen is not possible. In such events, cab provides an external control panel of the same functionality. HTI integrates such panels optically and functionally appealing external to the printer on the outside of a X-TubeProcessor Smart.
- SQUIX 4 installed horizontally to X-TubeProcessor
X-TubeProcessor Basic and SQUIX 4
The Basic is the smallest X-TubeProcessor. For tube labeling, cab SQUIX 4 printers are first choice. HTI makes use of peel-off devices. These separate printed labels automatically from their liner. Labels can thus be removed by hand or by an applicator, in this specific case a cylinder drive equipped with a pad. An extra-size metal plate ensures labels be handed over smoothly to the drive cylinder, which then moves with the label towards a tube, held by a gripper. The label is rolled onto the tube by rotation. Labeled tubes are finally inserted to a rack. Liner materials are wound internally on the SQUIX 4 printer.
Benefits of laser marking
The quality of sensitive goods depends, amongst others, on how they are stocked. Cells or functional cell structures, for example, can only be reliably preserved in the long term by using cooler systems and optimum stock temperatures as low as -200 °C. Only special label materials withstand such conditions. Instead, HTI selects for laser marking. This remains permanently visible on a vessel surface. If top markings, as well as highly performant and durable systems are required, the cab XENO 4 fiber laser is particularly economical. Optimally adapted to an operation, it is highly efficient and requires less energy than, for example, a CO2 laser. The center of a glass fiber forms the laser-active medium.
A XENO 4 consists of a control unit (beam source included) and the scan head, the latter connected to the beam source. Beam sources provide 20, 30 or 50 Watt output power. Highest beam powers are achieved by bundling, using a plano-spherical lens on the scan head. Such lenses allow specific marking fields be covered. HTI and its customers benefit from further advantages, such as focus on smallest spots and tubes be processed at high speed, as strongly bundled light must not overcome mechanical resistance. This results in markings as sharp as 1,000 dpi. They are proof to smudge and resist acids or alkalis, solvents and heat, cold and tear.
HTI Automation GmbH, Ebersberg, Germany, has been a specialist in lab and manufacture automation for more than 20 years. Business divisions include standard products for micro-screw tube processing as well as development services in lab technology.
Video of this application
HTI, specialist in lab and manufacture automation Opening, filling and labeling micro-screw tubes
Print and apply system HERMES Q
November 2022